

Engineering and Technology Quarterly Reviews
ISSN 2622-9374
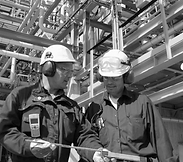


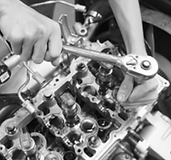



Published: 26 May 2020
Enhancing Physical, Mechanical and Thermal Properties of Rubberized Concrete
Raja Bilal Nasar Khan, Anwar Khitab
Mirpur University of Science and Technology, Pakistan
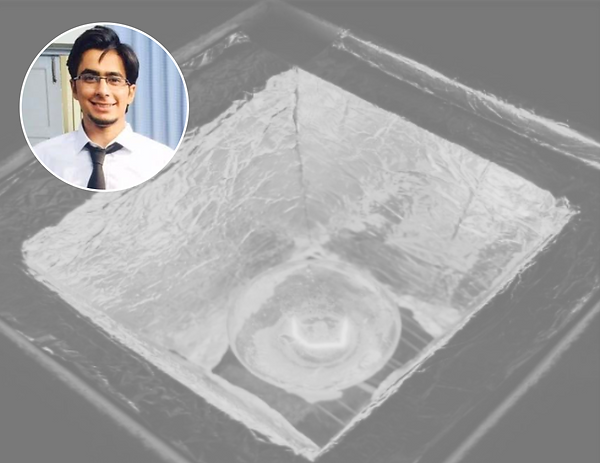
Download Full-Text Pdf

10.5281/zenodo.3852541
Pages: 33-45
Keywords: Concrete, Waste Rubber Tires, Thermal Conductivity, Density, Strength, Porosity
Abstract
This research aims to develop a low density concrete, characterized by high porosity and reduced thermal conductivity with slight to no compromise over strength, employing scrapped waste tires. Although, literature on the topic is available that addresses benefits and drawbacks of rubberized concrete, this experimental work was formulated to suggest an optimum dose of crumb rubber that imparts sufficient strength and workability in addition to insulation and low weight. Four types of specimens were cost and tested, containing 0, 5, 10 and 15% crumb rubber as partial replacement of sand in ordinary concrete, using ASTM standards. Specially constructed heat transfer measurement device was used to find out the thermal conductivity of the specimens. Scanning electron microscopy was carried out to examine the micro-structure of rubberized concrete. Results reveal that thermal conductivity and density lower by 30% and 15% respectively and porosity increases by 34% at 15% partial replacement of sand by rubber. Higher concentration of voids along the interface were observed at 15% replacement indicating poor bonding and a weaker ITZ, leading to reduced strength. Based on the results, 5% optimum dosage is recommended, which enhances porosity by 5%, compressive strength by 5.5%, and reduces slump by 16%, thermal conductivity by 16% and density by 2% respectively.
References
A.Sofi. (2018). Effect of waste tyre rubber on mechanical and durability properties of concrete – A review. Ain Shams Engineering Journal, 9(4), 2691–2700.
ABDOLLAHZADEH, A., MASOUDNIA, R., & AGHABABAEI, S. (2011). PREDICT STRENGTH OF RUBBERIZED CONCRETE USING ATRIFICIAL NEURAL NETWORK. WSEAS TRANSACTIONS on COMPUTERS, 10(2), 31–40.
Ahmed, S., Khitab, A., Mehmood, K., & Tayyab, S. (2020). Green non-load bearing concrete blocks incorporating industrial wastes. SN Applied Sciences, 2(2), 266. https://doi.org/10.1007/s42452-020-2043-6
Asadi, I., Shafigh, P., Abu Hassan, Z. F. Bin, & Mahyuddin, N. B. (2018). Thermal conductivity of concrete – A review. Journal of Building Engineering, 20, 81–93. https://doi.org/10.1016/j.jobe.2018.07.002
Aslani, F., & Khan, M. (2019). Properties of High-Performance Self-Compacting Rubberized Concrete Exposed to High Temperatures. Journal of Materials in Civil Engineering, 31(5), 04019040. https://doi.org/10.1061/(ASCE)MT.1943-5533.0002672
ASTM. (2013). ASTM C31: Standard Practice for Making and Curing Concrete Test Specimens in the Laboratory. Annual Book of ASTM Standards. https://doi.org/10.1520/C0192
ASTM C177-13. (2013). Standard Test Method for Steady-State Heat Flux Measurements and Thermal Transmission Properties by Means of the Guarded-Hot-Plate Apparatus. West Conshohocken, PA.
ASTM C192 /C192M. (2019). Standard Practice for Making and Curing Concrete Test Specimens in the Laboratory. West Conshohocken, PA.
Bakri, A. M. M. Al, Fadli, S. A. S. N., Bakar, M. D. A., & Leong, K. W. (2007). COMPARISON OF RUBBER AS AGGREGATE AND RUBBER AS FILLER IN CONCRETE. In 1st International Conference On Sustainable Materials 2007_ICoMS 2007. Penang, Malaysia.
Benazzouk, A., Douzane, O., Langlet, T., Mezreb, K., Roucoult, J. M., & Quéneudec, M. (2007). Physico-mechanical properties and water absorption of cement composite containing shredded rubber wastes. Cement and Concrete Composites, 29(10), 732–740. https://doi.org/10.1016/j.cemconcomp.2007.07.001
Benazzouk, A., Douzane, O., Mezreb, K., Laidoudi, B., & Quéneudec, M. (2008). Thermal conductivity of cement composites containing rubber waste particles: Experimental study and modelling. Construction and Building Materials, 22(4), 573–579. https://doi.org/10.1016/j.conbuildmat.2006.11.011
Bolden. (2013). UTILIZATION OF RECYCLED AND WASTE MATERIALS IN VARIOUS CONSTRUCTION APPLICATIONS. American Journal of Environmental Sciences, 9(1), 14–24. https://doi.org/10.3844/ajessp.2013.14.24
Elchalakani, M. (2015). High strength rubberized concrete containing silica fume for the construction of sustainable road side barriers. Structures, 1, 20–38. https://doi.org/10.1016/j.istruc.2014.06.001
Ghedan, R. H., & Hamza, D. M. (2011). Effect Of Rubber Treatment On Compressive Strength And Thermal Conductivity Of Modified Rubberized Concrete. Journal Of Engineering And Development, 15(4), 21–29.
Güneyisi, E. (2010). Fresh properties of self-compacting rubberized concrete incorporated with fly ash. Materials and Structures, 43(8), 1037–1048. https://doi.org/10.1617/s11527-009-9564-1
Hassan Riaz, M., Khitab, A., & Ahmed, S. (2019). Author’s Accepted Manuscript Evaluation of Sustainable Clay Bricks Incorporating Brick Kiln Dust Evaluation of Sustainable Clay Bricks Incorporating Brick Kiln Dust. Journal of Building Engineering. https://doi.org/10.1016/j.jobe.2019.02.017
Herrera-Sosa, E. S., Martínez-Barrera, G., Barrera-Díaz, C., Cruz-Zaragoza, E., & Ureña-Núñez, F. (2015). Recovery and Modification of Waste Tire Particles and Their Use as Reinforcements of Concrete. International Journal of Polymer Science, 2015, 1–8. https://doi.org/10.1155/2015/234690
Jalil, A., Khitab, A., Ishtiaq, H., Bukhari, S. H., Arshad, M. T., & Anwar, W. (2019). Evaluation of Steel Industrial Slag as Partial Replacement of Cement in Concrete. Civil Engineering Journal, 5(1), 181–190. https://doi.org/10.28991/cej-2019-03091236
Kaloush, K., Way, G. B., & Zhu, H. (2005). Properties of crumb rubber concrete. Transportation Research Record: Journal of the Transportation Research Board, 1914, 8–14.
Khalid, A. R., & Hameed, M. H. (2015). RUBBERIZED CONCRETE (RUBCRETE) A NOVEST APPROCH. In 1st International Multi-Disciplinary Conference. Gujarat, Pakistan.
Khatib, Z. K., & Bayomy, F. M. (1999). Rubberized Portland Cement Concrete. Journal of Materials in Civil Engineering, 11(3), 206–213. https://doi.org/10.1061/(ASCE)0899-1561(1999)11:3(206)
Khitab, A. (2012). Materials of Construction. Allied Books.
Khitab, A., Lorente, S., & Ollivier, J. P. (2005). Predictive model for chloride penetration through concrete. Magazine of Concrete Research, 57(9). https://doi.org/10.1680/macr.2005.57.9.511
Khitab, Anwar. (2005). Modélisation des transferts ioniques dans les milieux poreux saturés: application à la pénétration des chlorures à travers les matériaux cimentaires. Institut National des Science Appliquées de Toulouse. Retrieved from https://core.ac.uk/download/pdf/35285113.pdf
Khitab, Anwar, & Anwar, W. (2016). Classical Building Materials. In Advanced Research on Nanotechnology for Civil Engineering Applications (pp. 1–27).
Li, Y., Dong, W., Li, H., & Li, Z. (2015). Method of Vacuum Water Absorption to Determine the Porosity of Hardened Concrete. International Journal of Structural and Civil Engineering Research. https://doi.org/10.18178/ijscer.4.3.282-286
Marie, I. (2017). Thermal conductivity of hybrid recycled aggregate – Rubberized concrete. Construction and Building Materials, 133, 516–524. https://doi.org/10.1016/j.conbuildmat.2016.12.113
Munir, M. J., Kazmi, S. M. S., & Wu, Y.-F. (2017). Efficiency of waste marble powder in controlling alkali–silica reaction of concrete: A sustainable approach. Construction and Building Materials, 154, 590–599. https://doi.org/10.1016/j.conbuildmat.2017.08.002
Munir, M. J., Kazmi, S. M. S., Wu, Y.-F., & Patnaikuni, I. (2018). A Literature Review on Alkali Silica Reactivity of Concrete. International Journal of Strategic Engineering, 1(2), 43–62. https://doi.org/10.4018/ijose.2018070104
Oprişan, G., Enţuc, I.-S., Mihai, P., Toma, I.-O., Ţăranu, N., Budescu, M., & Munteanu, V. (2019). Behaviour of Rubberized Concrete Short Columns Confined by Aramid Fibre Reinforced Polymer Jackets Subjected to Compression. Advances in Civil Engineering, 2019, 1–11. https://doi.org/10.1155/2019/1360620
Riaz, M. H., Khitab, A., Ahmad, S., Anwar, W., & Arshad, M. T. (2019). Use of ceramic waste powder for manufacturing durable and eco-friendly bricks. Asian Journal of Civil Engineering. https://doi.org/10.1007/s42107-019-00205-2
Sohrabi, M. R., & karbalaie, M. (2011). An experimental study on compressive strength of concrete containing crumb rubber. International Journal of Civil & Environmental Engineering IJCEE-IJENS, 11(3), 24.
Topçu, İ. B., & Bilir, T. (2009). Experimental investigation of some fresh and hardened properties of rubberized self-compacting concrete. Materials & Design, 30(8), 3056–3065. https://doi.org/10.1016/j.matdes.2008.12.011
Toutanji, H. A. (1996). The use of rubber tire particles in concrete to replace mineral aggregates. Cement and Concrete Composites, 18(2), 135–139. https://doi.org/10.1016/0958-9465(95)00010-0
Xue, J., & Shinozuka, M. (2013). Rubberized concrete: A green structural material with enhanced energy-dissipation capability. Construction and Building Materials, 42, 196–204. https://doi.org/10.1016/j.conbuildmat.2013.01.005
Youssf, O., ElGawady, M., Mills, J. E., & Ma, X. (2014). PREDICTION OF CRUMB RUBBER CONCRETE STRENGTH. In 23rd Australasian Conference on the Mechanics of Structures and Materials (ACMSM23). Byron Bay, Australia.